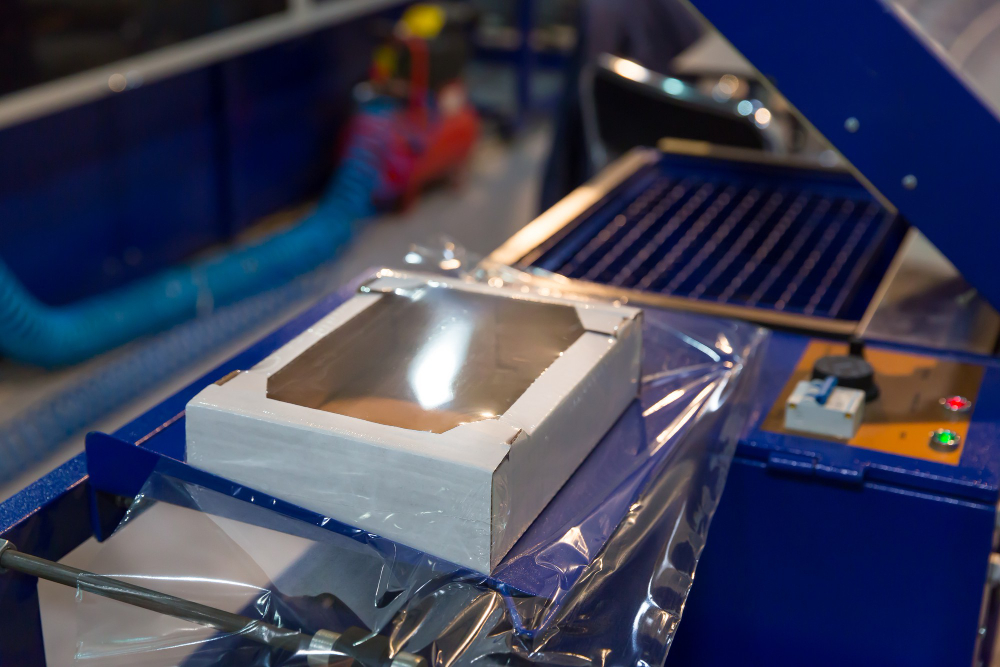
LVS Company: Plastic Blow Molding Services!
Plastic blow molding is a manufacturing process for creating hollow plastic parts like bottles, containers, and tanks. It’s commonly used across industries for products such as water bottles, chemical canisters, and fuel tanks. This process involves inflating heated plastic inside a mold to form the desired shape.
Key Steps in Blow Molding:
- Material Feeding: Plastic pellets are loaded into the machine hopper.
- Extrusion: Heated plastic is extruded into a tube (parison).
- Clamping: The mold closes around the parison.
- Blowing: Air inflates the parison to conform to the mold’s shape.
- Cooling: Chilled water circulates through the mold to solidify the part.
- Trimming: Excess material (“flash”) is trimmed for a clean finish.
Benefits of Plastic Blow Molding:
- Ideal for Hollow Parts: Perfect for items not feasible with injection molding.
- Cost-Effective: Highly efficient for producing large volumes.
- Flexible Designs: Accommodates complex geometries and various material options.
- Automation-Driven: Reduces manufacturing costs and ensures consistency.
Applications of Blow Molding:
- Bottles: For water, soda, oil, milk, and chemicals.
- Canisters: Used for fuel, chemicals, and water storage.
- Barrels and Tanks: For industrial or domestic use.
- Toys & Sporting Goods: Lightweight and durable plastic products.
Why Choose LVS Company for Blow Molding?
- Custom Solutions: We manufacture unique, tailored blow molding applications when standard products don’t fit your needs.
- Expert Engineering: Decades of experience in tooling, design, and manufacturing.
- State-of-the-Art Technology: Advanced blow molding machines ensure precision and quality.
- Comprehensive Services: From design to trimming, we handle the entire process with care.